Barite ilmenite hematite or manganese tetra oxide to increase slurry density-Bentonite pre-hydrated or dry hollow glass spheres or pozzolans to reduce density or increase cement yield cemented volume per volume of cement -Microsilica or latex to make the cement slurry gas tight-Silica flour to make the cement tolerant for temperatures above 110 C-Flexible. The simpler the better.
Concrete Mix Design Used For Laboratory Tests Download Table
Works by viscosifying the mix water or by plugging the pore throat in the filtrate cake with long polymer chains.
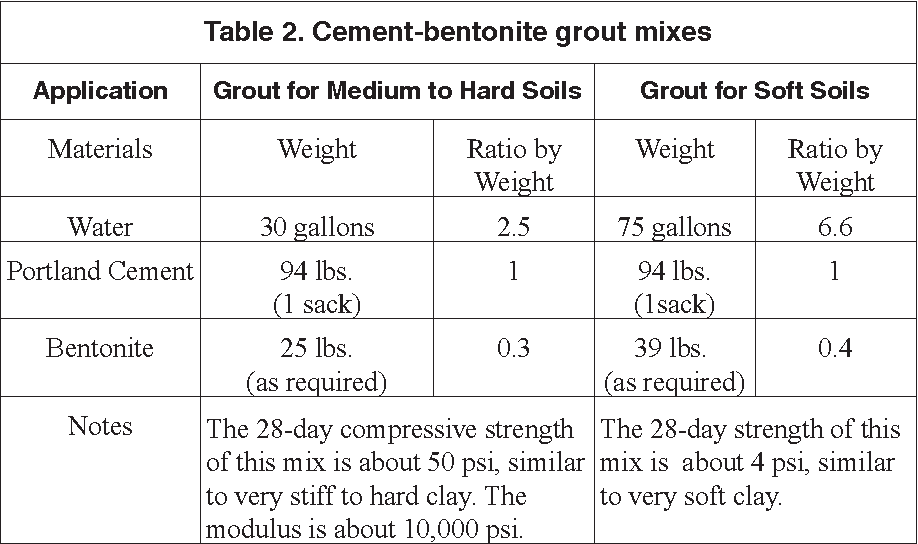
. Cement bentonite mix design You will need a steady hand for this eye catching nail design however its oh-so worth it. Step one adds the water choosing ratio mass. Day ÄBSTRÄCT Ä cementbentonite CB slurry cutoff wall is a variation of the slurry wall process that is used to create an underground barrier to stop the lateral flow of ground water and other fluids.
The primary effects of the cement admixtures on the physical properties of the cement either as a slurry or set are presented in Table 2. 6 rows bentonite powder. Ps pw 1 C CGp 1 where pw is the specific gravity of the mixing water assumed to be 10 and Gp is the grain specific gravity of.
Bag of cement yields 882 gallons of slurrybag for neat cement slurry to be used in grouting wells. INTRODUCTION If the natural soil does not meet the requirements of the. Source water was poured into the mixer and the mixing blade was turned on then bentonite was added.
The following table is the minimum acceptable amount of cement per ft. The finished wall creates a thin groundwater barrier with low permeability. In this method the trenches are excavated under a slurry that later solidifies and.
Fluid Loss Additives Fluid loss material is added to the cement slurry to help minimize the loss of water from the slurry into the formations. Data are presented from design mix studies and field-testing programs to. The table also includes an indication of the primary uses and benefits along with the cements that they can be used with.
It constitutes a mixture of bentonite slurry. The density of slurry ps is related to the concentration C of bentonite by weight of mix water as follows. Structural and technological criteria are required to design the bentonite-cement slurry composition.
Soil-Cement-Bentonite SCB slurry walls have been used with increasing frequency in recent years to provide barriers to the lateral flow of groundwater in situations where the strength of a normal soil-bentonite wall would be inadequate to carry foundation loads. There is a principle that I have always come to appreciate when talking about designing cement slurries. The monophase cut-off construction process was possible by application of a sodium salt mix to modify the properties of the slurry.
A slurry is a thin sloppy mud or cement or in extended use any fluid mixture of a pulverized solid with water often used as a convenient way of handling solids in bulk. 1 x 10-10 NA NA 7-14 Depth Limitations. The C-B slurry coats the sides of the trench with a thin slippery layer known as a filter cake.
Table assumes no formation loss. Bentonite slurry is a combination of sodium bentonite and slurry. This combination is frequently utilized to form a solid protective barrier in the ground.
The C-B slurry is prepared by combining cement with a hydrated bentonite-water mixture just before discharge of the C-B slurry into the trench. Cement plus Bentonite Selected for reducing slurry density and increasing slurry volume Normal bentonite additions range from 1 to 12 percent by weight of cement bwoc For every 1 bentonite bwoc added the water content must be increased 065 gallons assumes dry blending Bentonite reduces resistance of cement to. A vibratory hammer is used to drive special steel beams to design depth along the wall alignment.
The penetrations are overlapped to construct a continuous barrier. Mix Design Rules In order to keep field procedures simple the emphasis. CEMENT-BENTONITE SLURRY WALL MIX DESIGN Christopher R.
100 69-72 6-12 Self-hardening slurry Impermix. Soil-Cement-Bentonite SCB slurry walls have been used with increasing frequency in recent years to provide barriers to the lateral flow of groundwater in situations where the strength of a normal soil-bentonite wall would be inadequate to carry foundation loads. 100 69-72 8-16 Self-hardening slurry Composite wLiner.
CEMENT ONLY No Bentonite TABLE. The bentonite slurry had a viscosity of 47 MFV seconds and a density of 6458 pcf. Pump Pump Type 316 progressing cavity OutputPressure variable up to 20 gpm 261 psi Colloidal Mixer Mix Tank 130 CF with bottom clean out Mixing Pump 2 x 3 x 6 diffuser- type.
R an Steven R. In this context this means the use of the less possible additives in their lowest effective concentration that can provide the desired cement slurry. The bentonite slurry was mixed in a Hobart mixer.
Cement bentonite slurry mix design Written By symons Tuesday April 5 2022 Add Comment The ideal partner for tank-mix or ready-mix with established and new products. This is a quick reference and individual additives in a given category may not agree in total with the. When mixing on site its imperative to get the water volume with cement powder content right.
The mix resulted in 9 percent cementitious materials a watercementitious material ratio WC of 034 and 09 percent bentonite. Airfields and heavy-duty concrete pavement less than 10000 cubic yards. Cement Bentonite Mix Design.
Typically 21 ratio BentoniteCement. Bentonite cement earthfill sand unpermeable layer. Because of the relative simplicity.
A copy of mix design report and slurry properties are attached in Attachment B. The mixture including 10 bentonite 90 sand is the most economical solution that satisfies the limits values needed for clay core of earth fill dams and clay liners of solid waste storage areas. 5 x 10-7 50 95-120 5-10 Typically remote mix.
Recommended and acceptable filtration loss for various job are- For casing cementation ----- 100-200. The optimal cement slurry mix design principle. At 52 gallons of water per 94 lb.
This minimizes the slurry seepage out of the trench and groundwater seepage into the trench. 1 x 10-6 25 70-75 6-12 Self-hardening slurry. Quantity actually used may be rounded up to the nearest ¼ bag.
Slag cement-Bentonite 5 x 10-7. Data are presented from design mix studies and field-testing programs to. This principle is easy to remember.
Cement-bentonite slurry walls also provide another alternative. The cement-bentonite slurry is injected during penetration and removal of the beam. In general with bentonite cement slurry densities are from 115 to 150 ppg.
A bentonite cement slurry was applied to both cut-offs. A preparation method for cement bentonite slurry body preparation comprises the following steps. The final mix design consisted of 180 pounds of cement 51 pounds of flyash 2542 pounds of soil dry weight 50 gallons of bentonite slurry and 312 gallons of reservoir water.
Blend Mix Proportions And Blend Slurry Properties Download Table
All You Need To Know About Bentonite In Cement Slurries Better Well Cementing For All
Pdf Cement Bentonite Grout Backfill For Borehole Instruments Semantic Scholar
Sb Slurry Trench Cutoff Wall Schematic Lagrega Et Al 2010 Download Scientific Diagram
Soil Cement Bentonite Slurry Walls Geo Solutions Soil And Groundwater Problems Solved
Design Proportions For Sccb Mix Design Program Download Scientific Diagram
Pdf Designing Of Composition Of Bentonite Cement Slurry For Cut Off Walls Constructed By The Monophase Method
Pdf Cement Bentonite Grout Backfill For Borehole Instruments Semantic Scholar
0 comments
Post a Comment